Warehouse automation continues transforming the way industries do logistics by making them faster, better, and smarter. As technology advances, so do the ways companies optimize their workflows. From phasing out manual labor to enhancing goods-to-person (GTP) accuracy to improving storage environments for items that must be kept at cold temperatures, the future of supply chain management depends on warehouse automation.
Companies worldwide rely on automation to increase efficiency, save on expenses, and quickly adapt to customer expectations. Adopting advanced automation technologies supports companies that must stay competitive as online shopping surges, labor shortages increase, and more consumers demand sustainable operations.
Let’s look at some top trends in warehouse automation and modern logistics, like GTP systems, robotic picking, retrofitting older warehouses to newer ones, and automating deep freeze storage.
Table of Contents
Redefining order fulfillment in GTP systems
Because automation technology is revamping the picking and transporting of goods to workstations, warehouse workers no longer have to go through thousands of steps every day just to obtain products. Modern GTP systems use automated storage and retrieval to minimize transport time, better use warehouse floor space, and drastically reduce processing errors.
GTP systems also save time and energy on the warehouse floor by bringing products directly to the employees rather than the employees walking up and down the aisles to retrieve products. This feature of GTP systems is beneficial specifically for businesses that process high order volumes.
Also, GTP automation has had a positive impact on employee well-being. With less physical strain from walking and carrying heavy items, GTP systems create a more ergonomic workplace. Employees are less exhausted from manual labor and have more energy for thoughtful decision-making.
GTP solutions may include shuttle systems, conveyor belts, or robotics to move products, depending on the industry. Others may use vertical lifts or carousels to pick items accurately. All of them, however, have these benefits in common:
- Increased productivity: Less physical movement by employees leads to more order fulfillment in less time.
- More accuracy: Automated storage and retrieval systems (AS/RS) reduce human error because of more precise picking technology.
- Scalability and flexibility: GTP systems can adapt as the business grows so companies can adjust to seasonal surges in orders without compromising operational efficiency.
Ultimately, retailers around the globe using GTP automation experience faster and smarter operations and better workplace conditions. Employees are happier, leading to higher retention rates and more quality work. This delivers on the customer side, too, as they’re experiencing more rapid and error-free order deliveries. Because of improvements like these, GTP systems have become key to the success of warehouse logistics.
Robotic picking for enhanced accuracy and speed
Designed to pick individual items in high-SKU settings, robotic picking systems are quickly advancing because of rapid developments in artificial intelligence (AI) and machine learning. Enhanced with decision-making capabilities and gripping features, robotic piece-picking technology can pick up various items, like fragile pieces or perishables.
The perks of robotic piece picking include the following:
- Less dependency on manual labor: Lower costs, less labor shortage, lower risk of human error.
- Picking precision: AI-enhanced sorting means more order accuracy.
- More adaptability: Programmable robots can be adjusted to handle different product types in various settings.
As AI becomes more sophisticated, robotic picking solutions will keep getting smarter and easier to integrate, drastically improving overall automated warehouse operations.
Retrofitting to modernize existing warehouses
Building a fully automated warehouse takes a lot of time and is a costly investment, so understandably, not every business can afford to build one from scratch. Instead, businesses can turn to retrofitting as a solution. Automation retrofit technologies enable companies to take advantage of all the benefits of automation by integrating the features within existing infrastructure, minimizing downtime to current operations.
Many companies have already invested significantly in their current warehouses, so starting from square one isn’t an option financially or practically. Retrofitting is the perfect solution–it entails automated solutions like conveyor belts, autonomous guided vehicles, robotic picking systems, and warehouse management system (WMS) technology upgrades.
Before using retrofit options, businesses should consider the following:
- Compatibility: Ensure automation add-ons will smoothly integrate with existing WMS and workflows.
- Future-proofing: Choosing automation features that can adapt as the business expands.
- Return on investment: Asking what the cost of implementation will be and estimating any long-term savings.
Aside from cost, retrofitting solutions are also an excellent option for businesses looking to gradually bring in automation technologies rather than implement them all at once. By modernizing a warehouse at a slower, steadier pace rather than building a new one, companies have the flexibility to see how certain automation technologies will work for their individual needs, all while maintaining current operations.
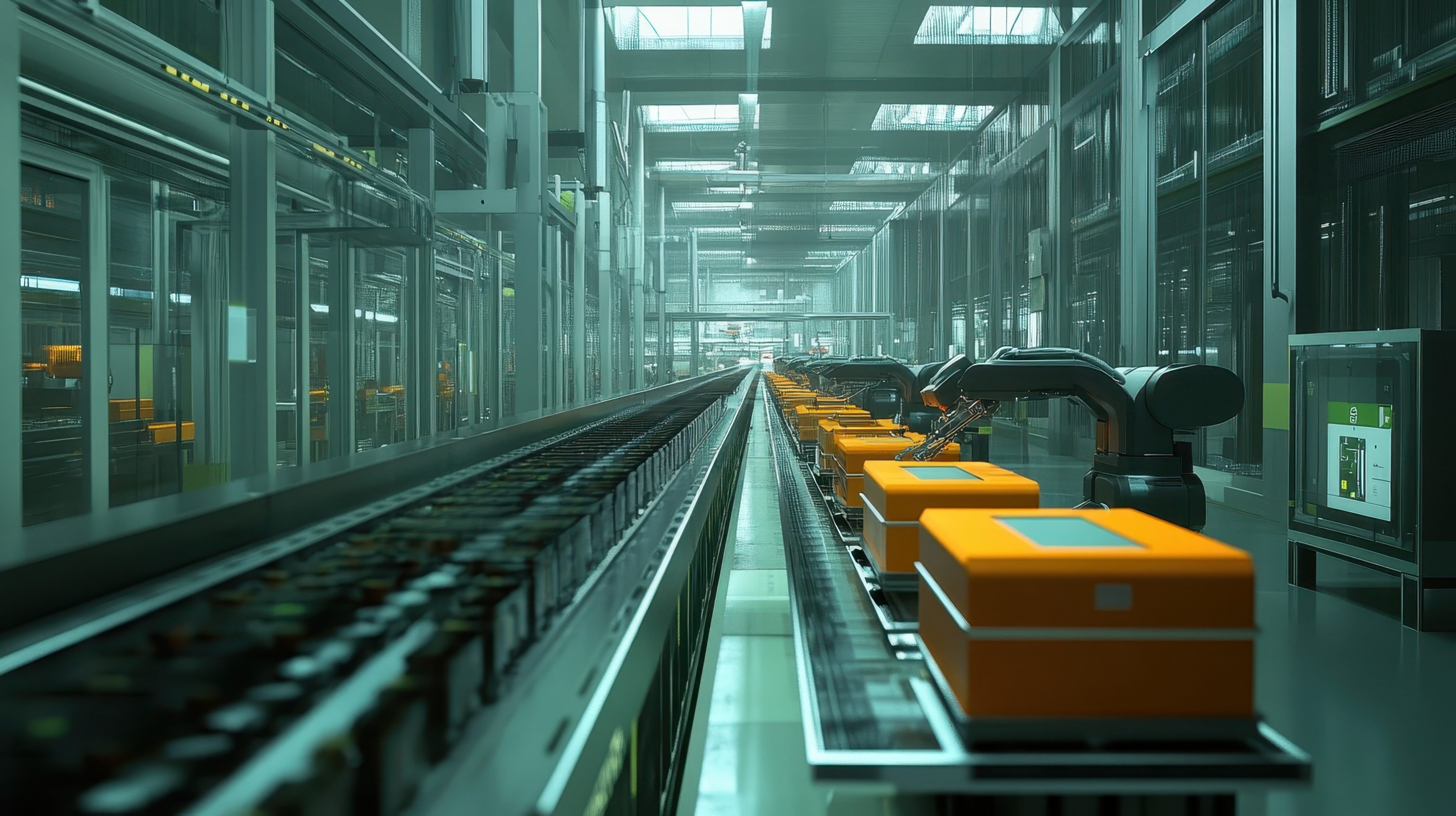
Overcoming supply chain challenges in icy temperatures with deep freeze storage automation
Storing frozen food is one of the biggest hurdles in grocery logistics. The ice-cold temperatures required to keep frozen food safe can cause physical distress for employees. Because of this, grocery and food retailers increasingly use warehouse automation technologies to keep products frozen while complying with safety regulations.
Deep freeze storage operations have unique challenges: reduced battery life for electronic parts, more wear and tear on equipment, and safety risks for human workers due to extended exposure to cold temperatures. Automation, however, can withstand freezing conditions and the challenges that come along with them.
Benefits of automation for deep freeze storage include:
- Robots and AGVs don’t mind the cold: Although traditional robots and automated guided vehicles (AGVs) don’t handle freezing conditions well due to the harmful effects of condensation, today’s deep freeze-friendly robots are built with insulation, lubricants, and more durable batteries for smoother operation.
- Automated storage and retrieval systems (AS/RS): Designed to maximize space usage, improve picking accuracy, and reduce the need for human interaction, these systems enhance worker safety and ensure operational consistency.
- Energy-efficient designs: To maintain subzero temps, deep freeze storage facilities use vast quantities of energy. However, when warehouses are designed to accommodate high-density storage and automated doors that control temperature changes, this reduces energy waste and improves storage efficiency.
Deep freeze automation can require a more significant investment but ultimately save businesses time, resources, energy, and expense. Reducing the need for manual labor makes for a safer workplace while improving order fulfillment accuracy. Deep freeze storage automation also allows for 24/7 operations. This is a significant benefit when rapid order delivery is crucial, especially for businesses like grocery and pharmaceutical companies.
The future of warehouse automation
Today, warehouse automation is more than just efficient–it’s strategically essential for staying competitive. Consumer demands will continue to evolve, expecting even faster and more reliable order delivery.
Here are a few key factors shaping the future of warehouse automation:
- AI-based decision-making: Smart technology that forecasts consumer demands to optimize logistics.
- Sustainability efforts: Automation that uses less energy to run daily operations and reduces the business’s carbon footprint.
- More human-machine synergy: Automation cannot fully replace humans, but it will enhance their output and complement their workflows if used correctly. This enables employees to focus on more critical tasks and make better, more thoughtful decisions.
Businesses must find the right automation solutions for them–solutions they can customize to fit their needs, whether building a new facility from scratch or integrating retrofit technology and expanding over time.
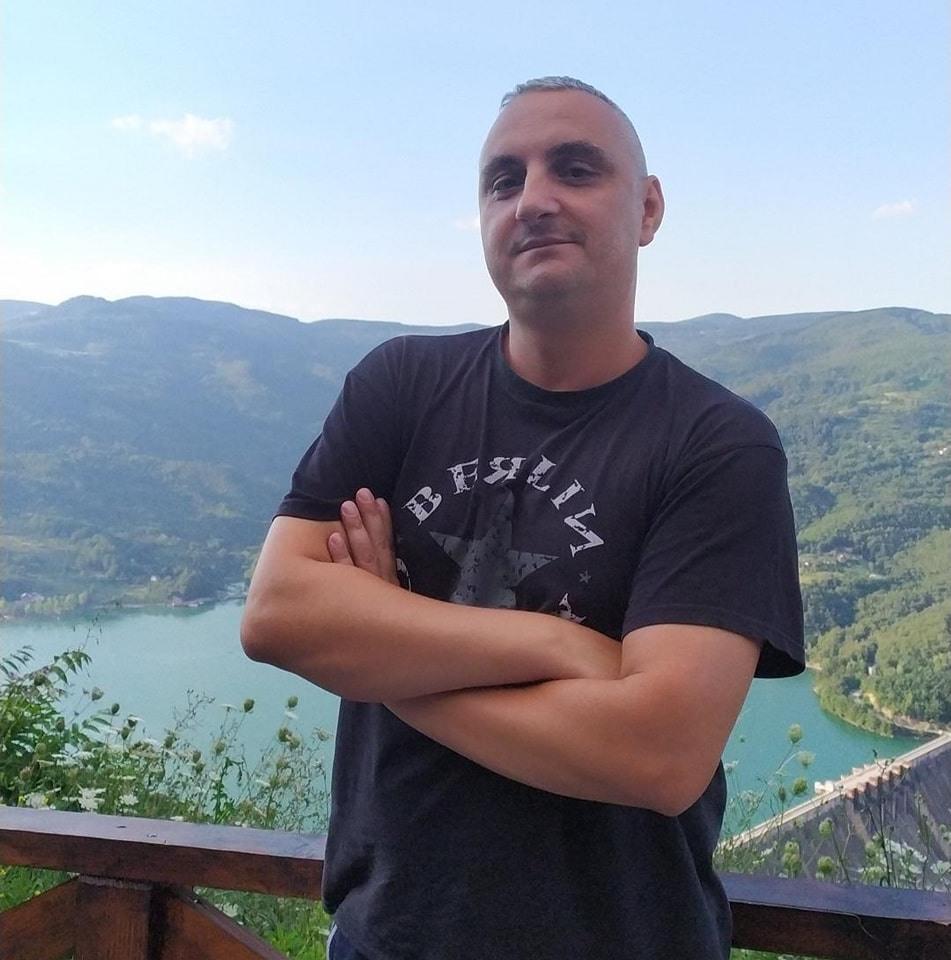
Andrej Fedek is the creator and the one-person owner of two blogs: InterCool Studio and CareersMomentum. As an experienced marketer, he is driven by turning leads into customers with White Hat SEO techniques. Besides being a boss, he is a real team player with a great sense of equality.